Durable, Slip-Resistant Surface Protection for Commercial Projects
The Skudo Commercial System protects surfaces from construction site damage and spills on large commercial projects. The innovative design forms an extremely tough outer skin that temporarily adheres to your surface, preventing dirt, debris, and grime from getting underneath.
The system consists of two layers:
- A water-based liquid Base Coat – sold in 5-gallon buckets
- A coated Heavy Traffic (HT) Commercial Mat – sold in 800 square foot rolls.
The Skudo Commercial System is applied by pressing the Commercial Mat into the wet Base Coat, which creates a heavy-duty, slip-resistant barrier that adheres to your protected work surface. Once the job is complete, the Skudo Commercial System simply peels away as one from the substrate and can be disposed of as general waste.
Benefits of Use
Skudo products provide protection against:
- Machinery, carts, ladders, and lifts
- Scaffolding and shoring
- Impact from foot traffic and dropped materials
- Water
- Spills and stains, including paint, mortar, coffee, cola
- Rust
- Mild solvents
- Mud, dirt, and debris
- Slip and trip hazards
- Mold & Bacteria (Select Products)
- UV (Select Products)
- Fire and welding sparks (Select Products)
Assessment & Suitability
Substrate Suitability
The Skudo Commercial System is the ideal protection for Concrete (cured 14+ days), including sealed and polished concrete and raw light-broomed finish or steel-trowelled concrete.
The Commercial System is also a great fit to protect Terrazzo flooring as well.
Limitations
The Skudo Commercial System is not suitable for certain substrates, including but not limited to:
- Transparent substrates where UV can affect the Base Coat
- Most linoleums and vinyls – the pH of the Base Coat can affect the surface
- High pH substrates (above 11.0) not neutralized (such as prior to a 14 day cure of concrete)
- Acid washed concrete
- Fibrous materials such as carpet, fabric or felt
- Rubber surfaces
- Painted substrates
- Unfilled travertine
- Pavers
- Unsealed hardwood
- White oak (hardwood)
- Substrates that have had other coatings applied that are not yet fully cured to their manufacturers specifications (such as densifiers, grouts, sealers, guards, epoxies, etc.)
- Weak or latex based grout on polished concrete
Preparation
- Ensure Skudo is suitable for the substrate on which it will be applied.
NOTE: Avoid applying Skudo Commercial System to unsealed hardwood, carpet, rubber, painted surfaces, weak or latex based grout, unfilled travertine, pavers, high pH substrates (above 11.0), linoleums and vinyls that are effected by high pH of Base Coat - Ensure the surface pH is below 11.0 and relative humidity (RH) is 90% or lower.
- Ensure the surface temperature is above 40’F and below 105’F.
- Do not apply the system externally if rain is likely within 24 hours.
- Ensure all densifiers, grouts, sealers, guards, epoxies etc. have been cured to their manufacturer specifications (touch dry is not sufficient).
- Ensure good ventilation.
- Ensure the area is clean and free from any foreign materials that will contaminate or compromise the Base Coat.
- Thoroughly sweep the surface to ensure the area is clean and free of debris/foreign materials that will compromise and contaminate the Base Coat.
Always spot test Skudo to specific job site conditions.
Base Coat Spread Rates
It is critical that the Skudo Base Coat be applied consistently to a thickness of at least 10 mils wet.
The spread rates of the Base Coat will vary due to weather and how porous the substrate is on which it will be applied.
- On flat sealed continuous substrates the Base Coat will yield approximately 130 sq. ft. per gallon.
- On raw concrete or substrates with a lot of undulation or grout lines the yield can significantly drop below the rate above.
- In colder climates warming the base coat in the sun or near a heater can yield better spread rates.
- When it is very hot, the applicator will need to be quick about laying the Mat on top of the Base Coat before it dries.
Due to unknowns and variables, Skudo can only recommend these figures as guidelines. Make sure to speak with a Skudo Representative to ensure adequate quantities are obtained to complete the job.
Note: The Base Coat can be used to adhere the overlap. This makes the system more water tight which is important for projects that have not been dried in yet.
After Application
Once applied, clear the area of any traffic and cordon off the area for at least 3 hours to allow the Skudo Commercial System to dry fully. Foot traffic is allowed after 3 hours, and machines can be used over the Commercial System the next day. Dry time may vary due to substrate temperature and porosity of the surface.
Remove any visible Base Coat after letting it completely dry, then peel it up. Any attempts to wipe up or press in the exposed wet Base Coat will negate its film-forming properties making removal extremely difficult. UV exposure degrades the peelability of the Base Coat.
Tools and equipment should be washed out using warm soapy water.
Although the Skudo Base Coat is classed as Non-Hazardous, avoid wash out entering drains, waterways, and finished surfaces. Please refer to the SDS for more information.
Patching & Maintenance
Should the Skudo Mats require patching, lift up the tear, apply fresh Base Coat underneath, and press the Mat back down. Alternatively, you may apply a new section of the Skudo Mat with Base Coat over the hole.
If the Commercial System is exposed to excessive standing water, extremely heavy rainfall, or drainage runoff, water can soften the Mat, breaking the bond between the protected substrate and Skudo Base Coat. If this occurs, normal lift traffic may damage the Mat. Drain or squeegee water off the affected area and attempt to keep traffic off the mat until it has dried. Once dried, the Mat will return to its original strength and, in most cases, will re-adhere to the substrate.
Removal
When ready to remove the Skudo Commercial System, work with a partner and simply lift a corner and peel it back at a 45-degree angle. To make the process easier and faster, nip the edge at 2 to 3-foot widths and tear it into thinner strips.
Dispose of the Mat in general site garbage bins.
Note: Removal of the Mat when the temperature is below 36’F makes the Commercial System less peelable.
The time it takes to remove the Skudo Commercial System will depend upon factors such as the texture of the surface it was applied to and whether or not there were any contaminants on the surface at the time of application.
RECOMMENDED: Use the Skudo Mat Puller to give more leverage and make the removal process easier on your hands.
Start with the Skudo Mat in a corner of the area to be covered.
Roll the Mat out 3 to 4 feet and align with a wall or edge of slab to ensure a straight roll out.
Lift the rolled out section over the rolled up portion of the Mat.
After soaking the Back Roller in Base Coat, begin applying the Base Coat directly onto the surface using the Notched Squeegee and Back Roller.
Make sure the Base Coat is applied in a consistent coat with a thickness of 10 Mils wet.
Apply it to the surface across the entire width of the Skudo Mat roll.
Note: Rough or textured surfaces will require a thicker application of Base Coat.
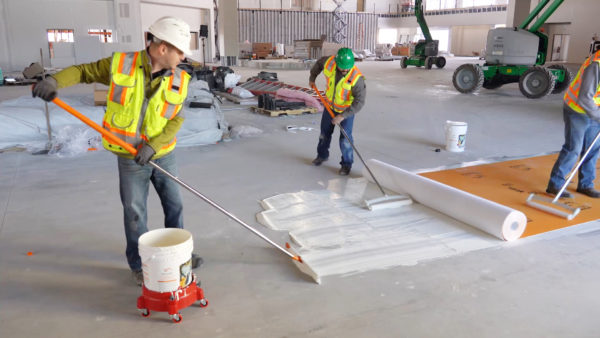
Lay the rolled out section of Skudo Mat back onto the wet Base Coat and press it in immediately, using either the Skudo Roller or a dry paint roller.
It is critical that the Skudo Mat is uniformly pressed into the Base Coat.
This now becomes the anchor for the rest of the roll.
Continue to apply the Base Coat again in front of the roll. When using the Skudo Notched Squeegee, ensure to pull the product away from the roll before back rolling.
Press in the Skudo Mat as you go, repeat process until the end of the row, taking note to ensure Base Coat thickness is 10 Mils wet. Once applied, do not lift the Mat.
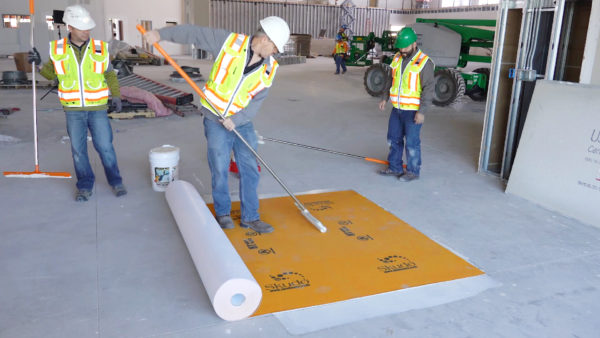
Start the next row with the Skudo Mat as per Step 1, overlapping the edge up to the guide line.
Roll out 4 to 5 feet of the Mat for alignment. This will ensure that the next section will be straight and will not drift off this line further down the area of application.